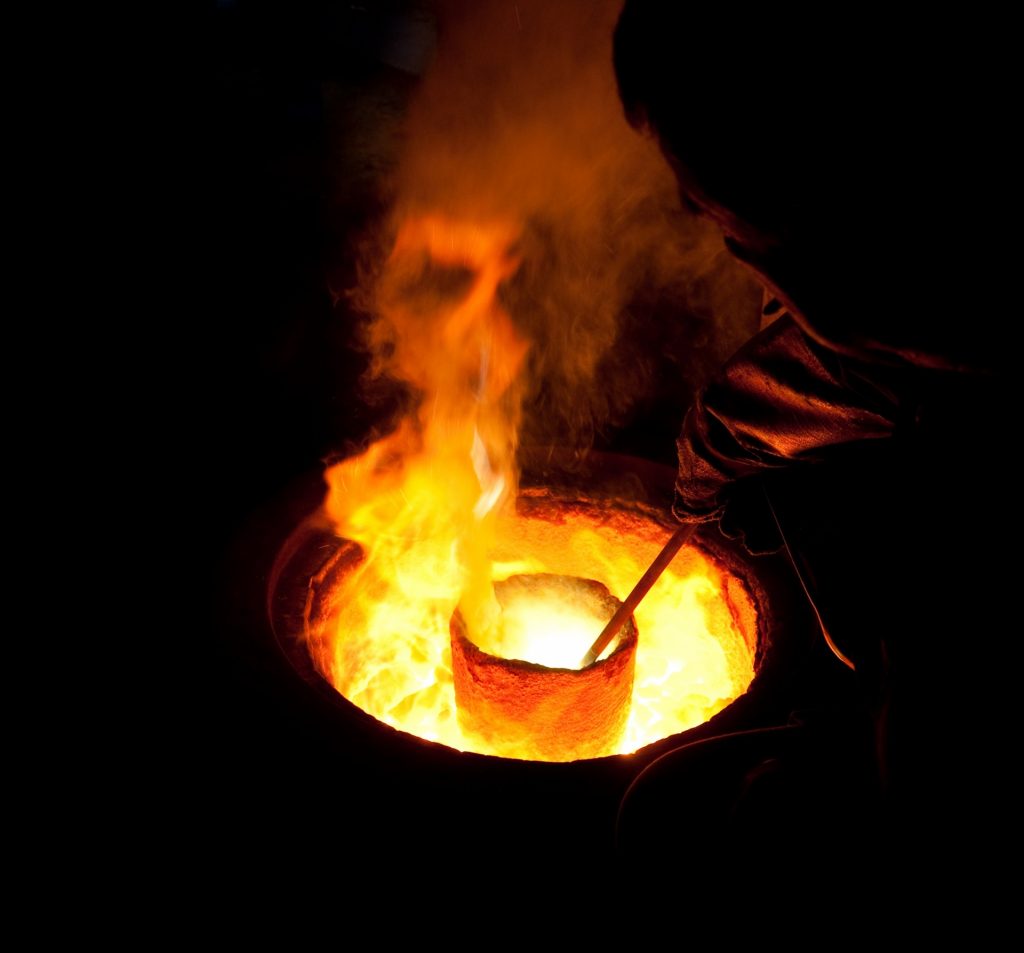
Fundamental properties of a solid material, such as electrical conductivity, magnetizability, mechanical strength, etc. define its possible application in commercial products. These basic characteristics depend on the chemical composition and microstructure of a material. The processing route of materials, especially the solidification from the liquid melt determines the materials microstructure. In order to achieve the desired microstructure in a reproducible way, the solidification process has to be well controlled.
Optimization of the solidification step helps to safe energy during the production process, reduces waste material and can safe time in industrial production. Furthermore, the final product can be lighter, stronger and save energy and material resources.
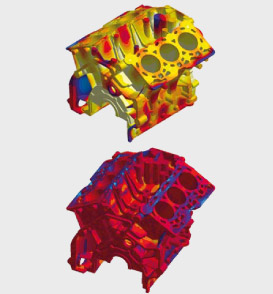
after the form is filled with liquid metal
(bottom) stress distribution during solidification
(by MAGMA GmbH, CC BY-SA 3.0)
Process Simulations
An advancement of alloy development is the application of simulations, predicting the microstructure formation during solidification processes, such as casting, welding, laser melting etc. Such simulation models can reduce cost and time in product development. However, good knowledge of material parameters in the liquid phase, concerning e.g. heat and mass transport, as well as the kinetics of crystal nucleation and growth are important for such simulations.
Therefore, precise measurements of thermophysical properties of liquid metallic alloys are important for useful casting simulations.
Due to the chemical reactivity of most metallic alloys in the liquid phase, precise measurements are often not possible with conventional, container-based methods.
Containerless Processing
The logic step is to use containerless methods, where the sample is not touching anything.
Electromagnetic levitation, a containerless method, offers the opportunity to obtain measurements that are not possible by conventional techniques. The absence of container walls enables the study of nucleation kinetics and the measurement of surface tension, viscosity, specific heat capacity and other thermophysical properties in the stable and undercooled liquid phase.
Processing under reduced gravity
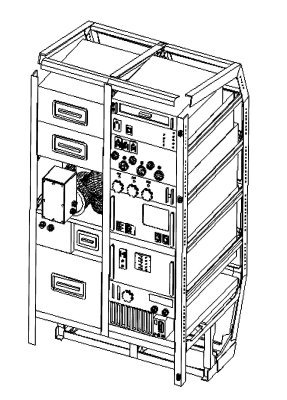
The need for the sample to be free of external forces during the measurements leads to the need for processing under reduced gravitational forces. The high forces needed on ground to lift and position a sample are high enough to lead to significant heating and turbulent flow in the liquid sample. In order to be able to control the fluid flow (laminar or turbulent), and to process the sample in a wide temperature range, reduced positioning forces and hence a reduced gravity environment is necessary.
Within the
ThermoProp/ThermoLab project, we make use of the measurement setup TEMPUS, available on board parabolic flights (TEMPUS) and the electromagnetic levitator ISS-EML which is located in the european science module ‘Columbus’ on board the International Space Station (ISS). More information on the ISS-EML can be found at ESA and at DLR.